Development Story, The T16
- Thom
- Jan 18, 2024
- 4 min read
When I made the Activist full suspension frame back in 2022, the intent was to make a big hitting park bike for myself.

While the thought of making them available for sale was present in the back of my head, it definitely wasn’t a driving factor in the design and development. The bike was to be thrown in the van to trip down to Wales and to hit the local lips here in Nottingham. It just so happened that the frame and bike came together in time for the Bespoked show and it seemed daft not to take it along. So it ended up getting thrown in the van and taken down to London.

The Activist grabbed quite a lot of attention as a steel single pivot on steroids. That’s exactly what I’d set out to make and riders seemed to be into it. So I set about reverse engineering it to offer the package in a range of geometry. Set sizes would have been simple enough but custom geometry and versatility is something that small scale makers can do that the big guys can’t. It’s our secret weapon, the trump card. I went through several iterations as I tried to shoe horn the original design into a parametric, configurable platform. All of them were great and yet each flawed in their own way regarding the important bit - custom configurations.
In design everything is compromise. Everything. I knew that I needed to be able to offer the frame with the same range of options as my hardtails but nothing I tried quite produced the balance of compromise I was happy with.
At the same time I started to consider my customer base and the intended use of the Activist. Primarily a park bike, I wondered is a hand made, small scale, customisable frame what park shredders need? To be frank, I don’t think so. While the durability of steel construction and repairability of the frame would suit the application well; the time and energy that goes into making a full suspension frame by hand, in small quantities, in the UK doesn’t. Despite how much I love the ride of that first Activist frame and how stoked I was that other riders liked it too, I think that most park rippers would probably be better served in grabbing a second hand frame made in the far east and riding it to death before repeating next season than they would commissioning an artisanal frame produced in the UK.
Experienced riders love steel frames for their ride character first and foremost. A close second is the classic look that only a steel frame can provide. I wanted to maintain everything that makes a great steel hardtail and somehow squeeze in a small shock to provide just enough travel to do pretty much anything. After all my Rallye and Eponym frames are designed to take anything you fancy giving them, and a full suspension version should follow suit. But to keep the same silhouette as the hardtails there wasn’t going to be much room for the shock so the leverage curve would have to be carefully considered. I’d need a well tuned suspension layout that punches above its weight.
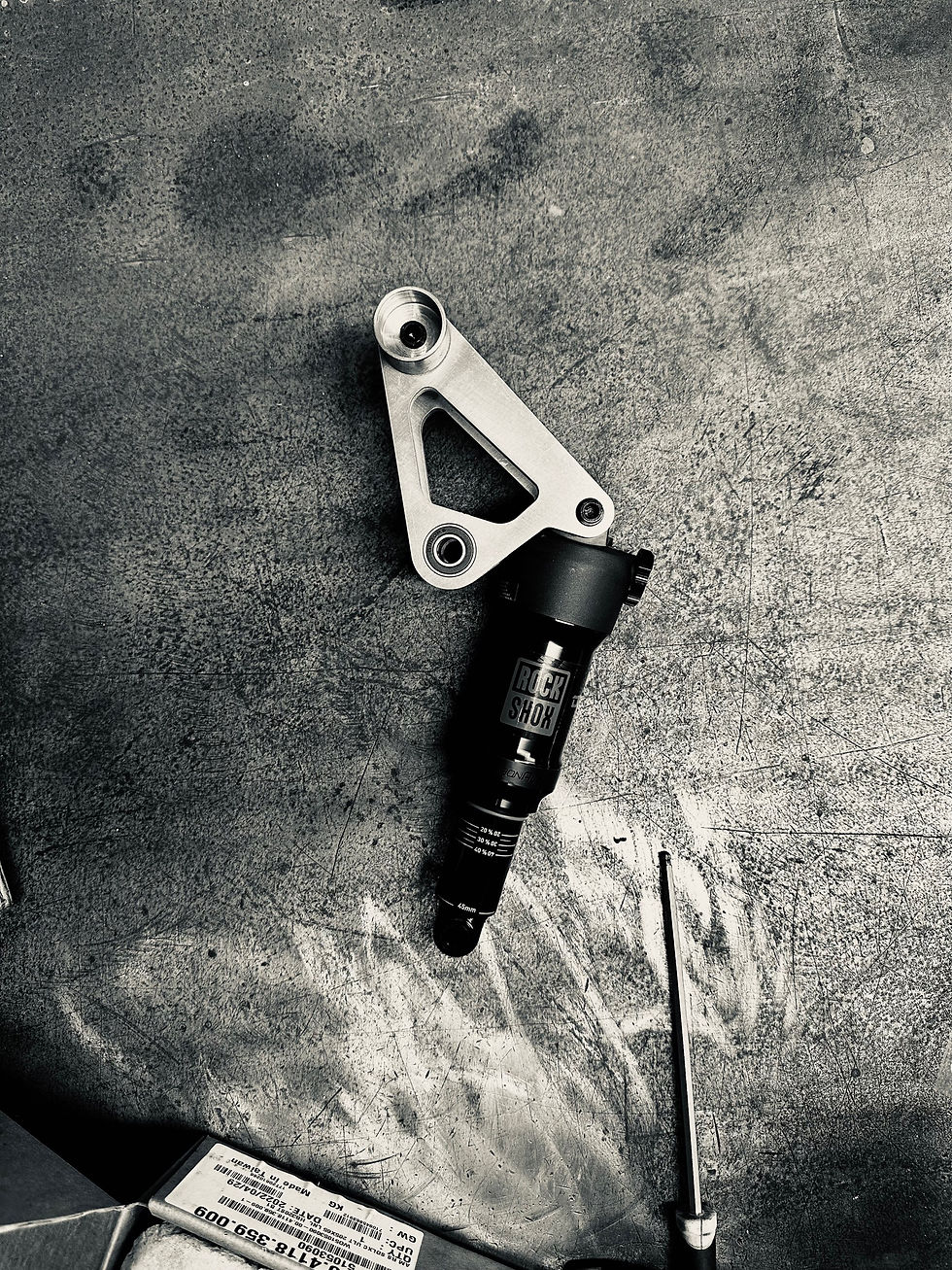
And speaking of weight, that was also a major factor. I believe weight does matter. Of course I’ve heard all the arguments, ‘1% this and take a poop that’ but no words have changed my feelings on the bike. Heavy bikes may have a place, my workshop isn’t it. But when building with steel and creating a linkage design the weight can begin to creep up because the linkage elements can’t always be as thin-walled as the tubing we use. So I’d need to somehow produce a linkage driven design without adding loads of pivots. Cue the flex stay. I’d seen a rise in the use of this design in the last few years and yet hadn’t spent a lot of time exploring the possibilities. To my surprise I found quite quickly that it was possible to create a layout that although technically a ‘flex stay’ actually had very little flex at all. This really got things going, I was in! All of a sudden I had a 120mm travel rear triangle that looked as though it might just do exactly what I wanted.
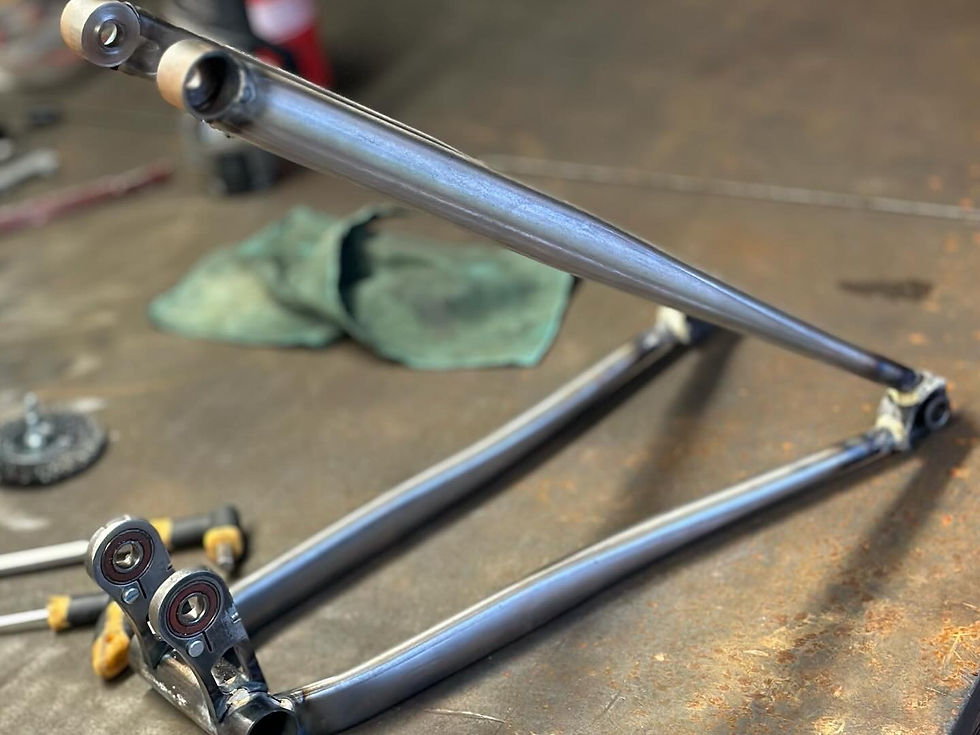
In order to allow for a full range of geometry options I still had to figure out how to avoid mounting the shock to the downtube. So I just mounted it to the seat tube. The lower section of the seat tube had to be made thicker anyway in order to house the main pivot and with the help of lasers and the magic of 4130 I could create a very strong mounting point. The short, stiff seat tube would be more than capable of the job, leaving the downtube free of the burden of supporting the rear axle and enabling me to use the same high end, triple butted tubes that make my hardtails so nice to ride. Holy shit. I think this is going to work!

I had the layout roughed out and I set about tweaking the leverage curve. When I was done not only was I happy with the suspension characteristics but the silhouette had gotten even closer to that of my hardtails. The anticipation for what might be was unbearable. So I spent every spare minute in the workshop making the first T16 frame. And since the design follows the hardtails so closely the workflow is also similar and the frame came together perfectly. There are a couple of elements that are definitely ‘prototype’ but crucially it is the realisation of the frame I’d spent my evenings drawing on the computer.

The brazing was still hot when I grabbed hold of the dummy axle and test-cycled the suspension. My thoughts were confirmed, you can barely feel the flex in the rear triangle happening. I’d be willing to bet that the same and more happens every time you hit a corner or stomp up a steep climb on any other bike.
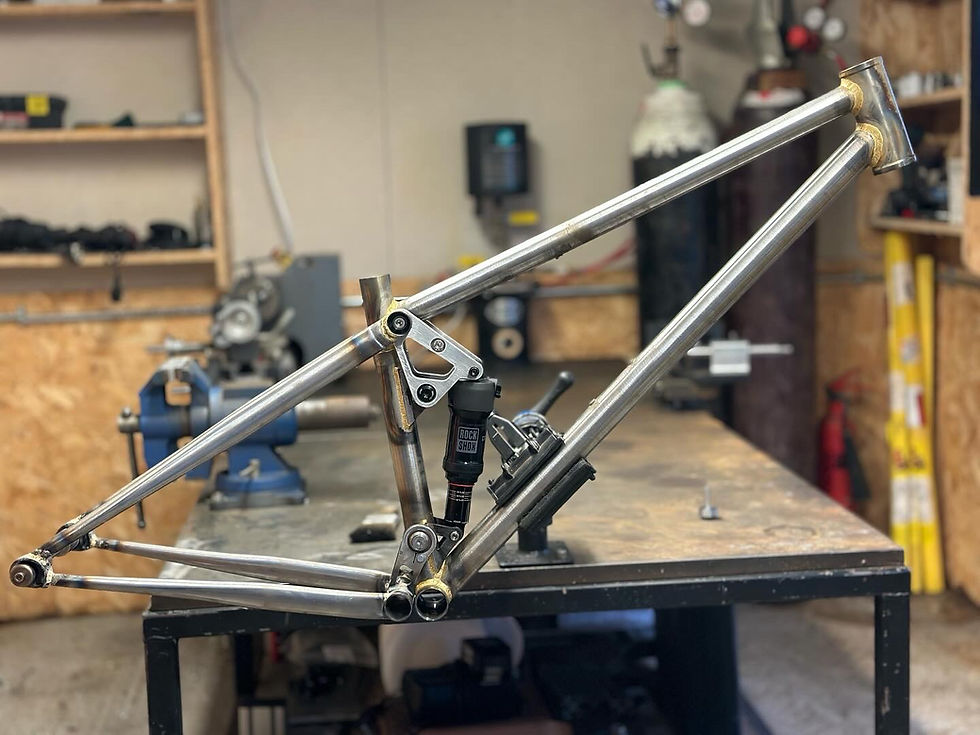
Yeah, this thing is sick. Am I aloud to say that? Just one final test remains and if it sucks I’ll let you know. But I’m really excited about what this little frame might be capable of.
And the Activist? I’m still so grateful for all the comments and interest in it. I’m just sorry it hasn’t quite materialised, yet…
Comments